Mazda National Distribution Centre recently embarked on a project aimed at enhancing the safety, comfort, and efficiency of their picking staff. As part of this initiative, they undertook the design and development of a new trolley system. Recognising the importance of ensuring the ergonomic suitability of the new trolley design, Mazda engaged Dohrmann Consulting, specialists in human factors, to conduct a comprehensive ergonomic assessment.
In this case study, we will delve into the collaboration between Mazda National Distribution Centre and Dohrmann Consulting to assess the ergonomic aspects of the newly designed trolley. Through this partnership, Mazda sought to optimise the working conditions of their picking staff, ultimately aiming to improve productivity, reduce the risk of workplace injuries, and enhance overall operational efficiency.
Our primary objective in this initiative was to Identify potential ergonomic risks associated with the use of the trolley, with particular focus on evaluating any excessive efforts required for pushing and maneuvering.
It is crucial that the assessment was conducted in the context of the actual work being done, with the various manual tasks performed by the picking staff to considered. As well as rate of picking, and maximum loads to be taken into account.
To achieve these objectives, our approach involved:
- Inspecting a prototype of the trolley available at the warehouse to assess its design features and functionality.
- Conducting precise measurements of the forces involved in manoeuvring the trolley, as well as evaluating the dimensions of the trolley and the width of the warehouse aisles to ensure ergonomic compatibility.
- Engaging in interviews with both picking staff and health and safety representatives to gather insights into their experiences, concerns, and suggestions regarding the trolley’s usability and safety.
- Reviewing relevant documents, such as preliminary engineering design of the trolley, existing safe work procedures, and Mezzanine floor layout to inform our assessment and provide comprehensive recommendations for optimising the trolley’s design.
We provided recommendations on the design of the trolley including optimal dimension of the top tray and box shelf, for efficiency and safe clearance of hand knuckles, amendments to the work safe procedure documents, and rules as well as a maintained program that identifies and repairs damaged or faulty trolleys.
By implementing these measures and adhering to the design specifications outlined in our recommendations, Mazda can confidently ensure the safety and well-being of their staff. This not only enhances workplace safety but also contributes to improved operational efficiency and employee morale. Our partnership with Mazda underscores the importance of prioritizing ergonomic considerations in design and underscores our commitment to supporting organizations in creating safe and conducive work environments.
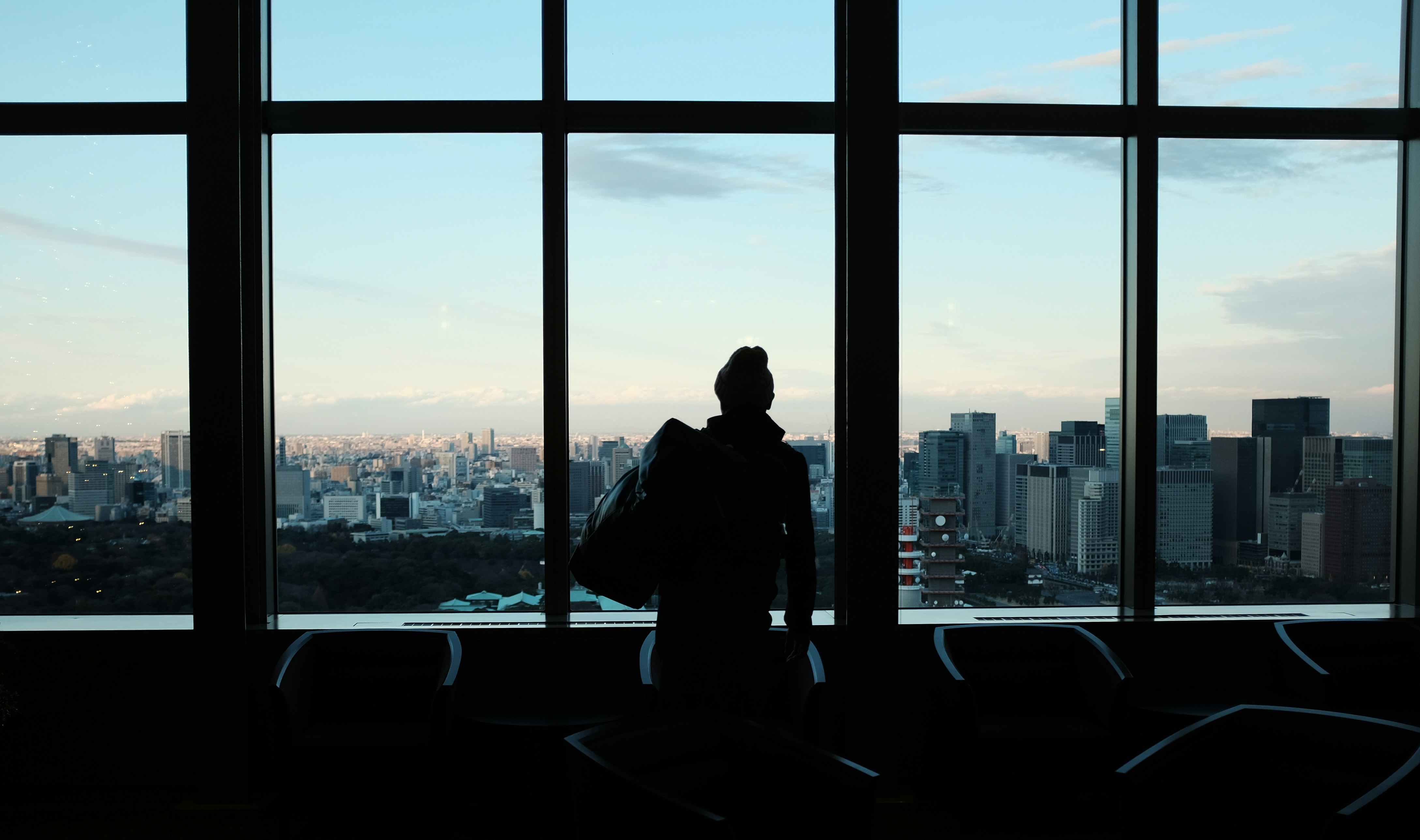